The wind turbine tower is made in a new way, and the transportation is more convenient!
Recently, Keystone, an American wind power tower manufacturer, announced the launch of the world’s first commercial production of a spiral welded tower project in Texas, USA.
The company claims that this welding method can effectively reduce the production and transportation costs of steel towers.
“Gigantic”
With the large-scale development of wind power, wind power equipment such as towers and blades are constantly becoming “giant”, and the transportation of large-scale equipment of tens of meters has become an urgent problem to be solved in the wind power industry. Wind power equipment manufacturers at home and abroad are actively exploring newer technology for wind turbine tower tube.
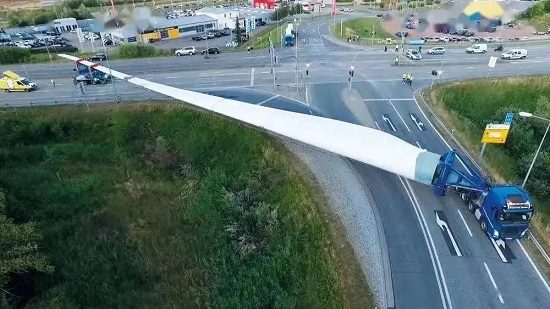
Wind turbine blades in transit
Breaking through the barriers
The spiral welded tower allows the construction party to carry out on-site welding and installation, and the steel plate material can be transported in the form of “flat”. The diameter of the tower is expected to reach 20 feet to 25 feet, or about 6.0 meters to 7.6 meters.
It is understood that this technology is an innovative project supported by the US Department of Energy, providing $7 million in research and development funding. The spiral welding method comes from the traditional steel pipe industry. The steel plates used to manufacture the tower are rolled into a cylindrical shape and then welded. Each steel plate is only a few meters long, which greatly reduces the difficulty of transportation.
Using spiral welding technology to manufacture wind turbine towers is 10 times faster than traditional steel towers, and can build towers of 160 meters and above while effectively controlling costs. This technology not only brings a new level of automation to wind turbine towers, but also helps to achieve net zero emissions goals.
Just like the technical breakthrough of lithium batteries in recent years, in order to provide the most advanced wind turbine towers, the company has cooperated with the world’s largest wind turbine manufacturer. Spiral welding enables faster tower production and higher quality. The company is planning expansion and expects to deliver the first commercial spiral welded towers this summer.
Reduce shipping risks
The tower is one of the main components of wind turbine equipment. Its function is to support the nacelle and the wind rotor to a suitable height, so that the wind rotor can obtain a higher and stable wind speed to capture more wind energy.
Traditional wind turbine steel towers are often transported as cylinders, which are often constrained by being too tall or too wide.
In order to reduce the cost of wind power generation, large-scale wind turbines have become a trend. At present, the single-unit power of China’s domestic onshore wind turbines is moving towards the era of 5 megawatts, and the offshore wind turbines have exceeded 10 megawatts. At the same time of the large-scale wind turbine, the larger-sized wind turbine equipment inevitably increases the difficulty of transportation.
Taking the blade as an example, the radius is very large, and the requirements for the road are very high, especially in special road conditions such as mountains and urban areas, transportation is difficult.
The taller the wind turbine tower, the more wind energy can be captured and more green electricity can be produced. At the same time, the power of a single wind turbine is increasing, which also puts forward higher requirements for the height of the hub, the diameter of the impeller and the size of other corresponding equipment. As the size of wind turbine equipment increases, transportation costs increase significantly.
Danish wind turbine manufacturer Vestas’ latest onshore wind turbine tower has a height of more than 160 meters and an offshore wind turbine blade length of more than 115 meters, constantly setting new industry records.
It is worth noting that in recent years, accidents in the transportation of wind turbine equipment have also occurred frequently. In the second half of last year, there was a collision between a semi-trailer train transporting wind turbine blades and another freight train in Texas, USA. Previously, there have been incidents in China, such as wind turbine equipment transport vehicles sweeping down house tiles when passing through residential areas, and towers overturning during transportation.
Lighter & stronger
Wind power equipment manufacturers not only innovated tower welding technology, but also began to work on materials. In April this year, General Electric, an American wind power manufacturer, announced that it would introduce 3D printing technology and use a “three-story high” 3D printer to produce concrete fan tower bases at wind power construction sites. The hourly consumption of concrete is expected to be More than 10 tons, it can “print” wind power towers over 20 meters on site.
Goldwind Technology, a leading wind power company in China, is also actively developing steel-mixed wind turbine towers, using a mixture of concrete bases and steel towers to ensure safe and reliable power generation while reducing transportation restrictions. On May 10, Goldwind announced that the company’s subsidiary Tianshan Hi-Tech Co., Ltd. participated in the formal implementation of two steel-concrete tower industry standards, which have become the latest standards for the production of this type of wind turbine tower.
Not only that, in terms of blades, many domestic and foreign wind power manufacturers have also stated that in order to meet the needs of large-scale wind turbines, they will develop and use lighter and higher-strength blade materials in the future, including carbon fiber and new resins.
In the face of the transportation challenges brought by the large-scale wind turbines, the wind power industry needs technological innovation, but it will take some time for large-scale promotion and application, and it will take more experiments and time to test which method can stand out in the end.