Lithium battery equipment overview
Lithium battery equipment generally refers to various manufacturing equipment used in the production process of lithium batteries. Lithium battery equipment has a significant impact on lithium battery performance and cost and is one of the determining factors.
The production process of lithium batteries is long, with more than 50 processes in the production process, and more than 50 types of equipment are needed to complete the manufacturing of each process. The process links determine that lithium battery equipment is complex and highly specialized.
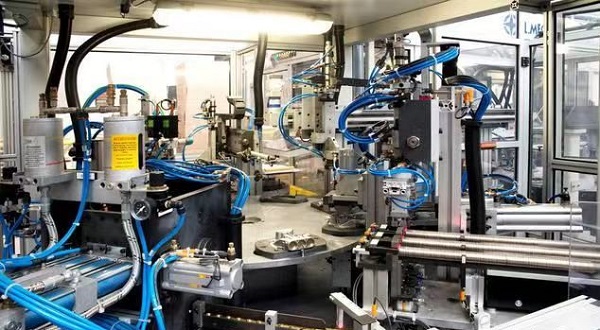
Lithium battery non-standard automation equipment
The manufacturing of various types of lithium-ion batteries can be divided into four process stages: electrode production, cell assembly, cell capacity grading & formation, testing and battery packaging.
The electrode manufacturing process includes stirring, coating, rolling, slitting, sheeting, tab forming and other processes. It is the basis for lithium-ion battery manufacturing and it plays an important role and there are very high requirements in the performance, accuracy, stability, automation level and production efficiency.
The cell assembly process mainly includes winding or lamination, cell pre-packaging, electrolyte infusion and other processes, which requires high accuracy, efficiency and consistency.
The battery cell activation and detection process mainly includes battery cell precharge & formation, capacity grading, etc.
The battery packaging process includes testing, classifying, and series-parallel combination of the individual cells that make up the battery pack, as well as testing the performance and reliability of the assembled battery pack.
Current status of lithium battery equipment industry
In the lithium battery industry, the barriers to lithium battery equipment for some simple processes are low, resulting in the current large number of lithium battery equipment companies. However, the concentration of the entire lithium battery equipment industry is still very low.
The future development of lithium battery equipment
Although China-made lithium battery equipment has made great achievements, the technical level of China-origin equipment is still relatively weak so far, and the degree of automation is not high. Some large battery manufacturers still need to import equipment.
As power lithium batteries become the focus of lithium battery development, the automation and intelligence of lithium battery equipment have become inevitable requirements. Only the declining price of electric vehicles can promote consumption, which also determines that the great development of EVs will inevitably require the cost of power batteries to be continuously reduced.
There are two ways to reduce the cost of power batteries. One is to use new material combinations to increase energy density. The second is to achieve scale effects and reduce costs through mass production.
Fully automated and intelligent lithium battery production equipment, based on the improvement of lithium battery production technology, enables the produced lithium batteries to have better consistency, highly reliable safety performance and high yield, thereby reducing production costs. This puts forward higher requirements for lithium battery manufacturing equipment.
In the future, equipment manufacturers will need to join forces with battery manufacturers to build automated and intelligent production lines.
Global landscape of lithium battery industry
The global lithium-ion battery industry is dominated by China, Japan and South Korea, accounting for about 95% of the global market share. Domestic companies have a relatively high share of China’s 3C consumer lithium battery market.
Japan and South Korea occupy high-end positions in the lithium battery industry, and are significantly ahead of Chinese companies in high-end consumer lithium batteries and power batteries, especially in the field of ternary and lithium manganate power batteries.
In recent years, China’s market share has maintained a steady increase due to the rapid development of new energy vehicles.
The industrialization of lithium-ion batteries began in Japan. With the growth of the lithium-ion battery industry, special equipment for lithium-ion batteries began to emerge.
In 1990, Japan’s Kaido Company successfully developed the first prismatic lithium-ion battery winding machine.
In 1999, South Korea’s Koem Company developed a lithium primary battery winding machine and a lithium primary battery assembly machine.
Japan’s Kaido and South Korea’s Koem are both companies with deep accumulation in electronic special equipment. The development of lithium battery special equipment is actually developed on the basis of capacitor equipment, and the two have technical similarities.
Today, the automated production equipment of many large battery factories are also purchased directly from Japanese and Korean companies.
In recent years, China has become the main base for global lithium battery production. With the development of lithium battery companies, the demand for lithium battery special equipment is also becoming increasingly strong.
Many major lithium battery equipment manufacturing companies entered the lithium battery equipment manufacturing industry around 2005.
In recent years, some outstanding lithium battery equipment companies have begun their journey of independent innovation, and the technical level of domestic lithium battery equipment is also improving rapidly.
The cost-effective advantage of Chinese lithium battery equipment
The biggest advantage of Chinese-made lithium battery equipment is still cost-effectiveness. Take a fully automatic winding machine as an example. The price of Chinese-made equipment is only one-fifth of that of similar equipment in Japan.
With the advancement of equipment technology in recent years, the cost-effective advantages of China’s lithium battery equipment have become increasingly obvious.
Some well-known lithium battery manufacturers have begun to consider domestic equipment, especially battery manufacturers like CATL and ATL who are actively adopting Chinese lithium battery equipment.
This also proves that Chinese lithium battery equipment can fully meet the current domestic lithium battery production requirements.