EVs are powered by electricity, and high-voltage wiring harness connectors are the core components responsible for tightly connecting various high-voltage components such as batteries, motors, and charging devices to achieve efficient transmission of electrical energy.
In the complex architecture of EVs, high-voltage wiring harness connectors are only a small component, but they play an extremely critical role and can be called the “power bridge” of EVs.
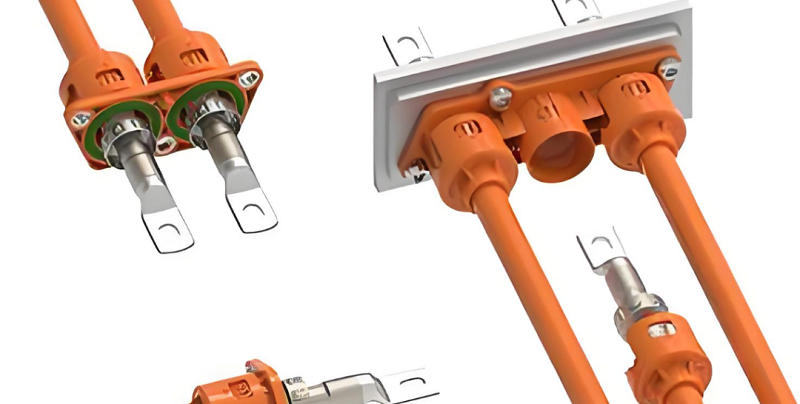
EVs high-voltage wiring harness connectors
High voltage withstand capability
The operating voltage range of EVs is usually between 60V and 1500V, far exceeding the 12V or 24V of traditional fuel vehicles.
Common pure electric vehicles generally have a high voltage of around 400V, and some models use 800V. Such a high voltage places high demands on the voltage resistance of high-voltage wiring harness connectors.
Once the voltage resistance of the connector is insufficient, it may cause insulation breakdown, causing serious problems such as short circuit and leakage, which will not only damage the vehicle’s electrical equipment, but also pose a huge threat to the life safety of the driver and passengers.
High-voltage wiring harness connectors must be able to withstand the highest voltage of EVs, and a certain voltage margin must be reserved to cope with special situations such as instantaneous overvoltage.
In order to meet high voltage requirements, high-performance insulating materials such as polyimide (PI) and polytetrafluoroethylene (PTFE) are used in the design of connectors.
These materials have excellent electrical insulation properties, which can effectively prevent current leakage and ensure the stable operation of connectors in high voltage environments.
High current transmission performance
In addition to high voltage, high-voltage wiring harnesses for new energy vehicles also need to transmit high current.
As the main energy transmission channel, the rated working current of its DC bus can reach more than 200A, and some high-power models can even be higher.
When large currents are transmitted, a large amount of heat will be generated. If the connector cannot effectively cope with it, overheating will occur, which will lead to increased contact resistance, further aggravating the heat, forming a vicious cycle, and eventually the connector may be damaged, affecting power transmission.
In order to cope with large currents, connector materials usually use metal materials with high conductivity and good heat dissipation performance, such as copper alloys.
Copper alloys have excellent electrical conductivity, which can reduce the resistance during current transmission, reduce energy loss and heat generation. At the same time, its good heat dissipation performance helps to dissipate the generated heat in time and maintain the normal working temperature of the connector.
In terms of structural design, the current density is reduced, the heat is reduced, and the current carrying capacity of the connector is improved by increasing the contact area of the connector. The connection method of the connector can also be optimized to ensure the tightness and stability of the connection, reduce the contact resistance, and ensure the smooth transmission of large currents.
Waterproof and dustproof standards
In the complex use environment of EV, high-voltage wiring harness connectors face challenges from various external factors, and waterproof and dustproof performance is crucial.
The protection level (IP level) is established by the International Electrotechnical Commission (IEC) and is an important standard for measuring the degree of protection of electrical equipment housing against foreign body intrusion. EV high-voltage wiring harness connectors are usually required to reach IP67 and above protection level.
High temperature resistance
During the operation of EV, the high-voltage wiring harness connector will generate heat due to the current transmission. In addition, the temperature of the vehicle engine compartment and other parts is high, so the working environment temperature of the connector is often very high.
Especially when charging at high power or driving at high speed, the current is large, and the heating problem of the connector is more prominent.
If the connector cannot withstand high temperature, problems such as material aging and deformation will occur, resulting in poor contact, affecting power transmission, and even causing safety accidents.
EMC Design of Connectors & plug-ins
In order to achieve good EMC performance, a series of measures need to be taken in the design of high-voltage wiring harness connectors.
- Shielding design is a key link. Metal materials such as aluminum alloy and copper alloy are usually used in the connector shell. These metal materials can form a shielding layer to isolate the circuit inside the connector from the external electromagnetic field, prevent the internal electromagnetic interference from radiating outward, and also prevent the external electromagnetic interference from entering the connector.
- Grounding measures are also very important. The connector will be connected to the EV’s grounding system through a special grounding pin or grounding wire to ensure that the shielding layer of the connector can be effectively grounded. In this way, when the connector is subject to external electromagnetic interference, the interference current can flow away quickly through the grounding path to avoid the accumulation of interference signals inside the connector, thereby ensuring the normal operation of the connector and the entire high-voltage wiring harness system.
Through reasonable shielding design and grounding measures, high-voltage wiring harness connectors can effectively reduce the impact of electromagnetic interference, improve the electromagnetic compatibility of EV vehicles, and ensure the stable and reliable operation of the vehicle’s electronic system.
Insulation design
Insulation design is an important part of the safety design of high-voltage wiring harness connectors. Its core purpose is to prevent current leakage, thereby ensuring the safety of personnel and vehicles.
In terms of material selection, high-voltage wiring harness connectors usually use materials with excellent electrical insulation properties.
- Cross-linked polyethylene (XLPE) has been widely used in EV high-voltage wiring harness connectors due to its good electrical properties and high heat resistance. It can effectively prevent current leakage in high-voltage environments and ensure that electrical energy is transmitted within the specified path.
- Silicone rubber is also a commonly used insulating material. It not only has excellent insulation properties, but also has good high and low temperature resistance. It can maintain stable performance in the temperature range of -50℃ to 200℃. This makes it perform well in dealing with the complex and changeable working environment of EV vehicles. Even in the hot engine compartment or the cold winter, silicone rubber can reliably play an insulating role and ensure the normal operation of the connector.
In addition to material selection, insulation structure design is also crucial. The insulation structure of the connector needs to be carefully designed to ensure reliable insulation protection under various working conditions.
For example, the insulation performance of the connector can be improved by increasing the thickness of the insulation layer, optimizing the shape and structure of the insulation layer, etc. Multiple insulation protection measures are also adopted, such as wrapping multiple layers of insulation material around the conductor to form a multi-level insulation barrier to further reduce the risk of current leakage.
High voltage interlocking structure
The high-voltage interlocking structure is an extremely important safety design in the high-voltage system of new energy vehicles. Its principle is to use low-voltage signals to monitor the integrity and continuity of the high-voltage circuit in real time.
In the high-voltage system of new energy vehicles, various high-voltage components are connected to each other through high-voltage wiring harness connectors to form a complex high-voltage circuit. The high-voltage interlocking structure is like a “safety guard” of this circuit, always monitoring the status of the circuit.
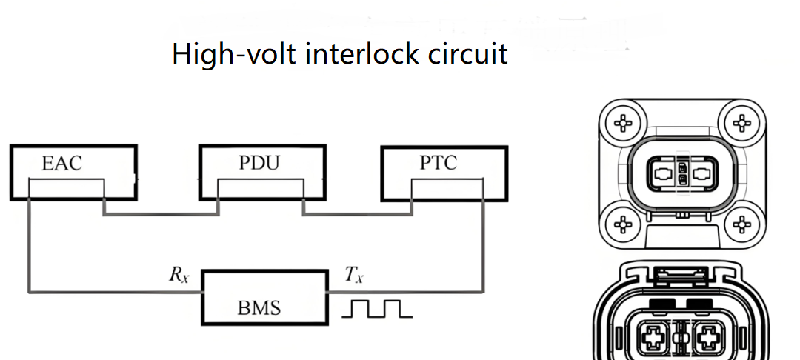
High volt interlock circuit
The high-voltage interlocking structure sets up special interlocking terminals in the connector, which cooperate with the high-voltage terminals. When the connector is connected normally, the interlocking terminals form a closed low-voltage signal loop.
Once the connector/plug-in is loose, falls off, or has abnormal connection, the interlocking terminals will be disconnected, and the low-voltage signal loop will be interrupted. At this time, the vehicle’s control system will immediately detect this change and respond quickly, such as cutting off the high-voltage power supply to avoid high-voltage electricity from causing danger to personnel and vehicles.
Take the vehicle driving process as an example. If the high-voltage wiring harness connector becomes loose due to vehicle vibration or other reasons, the high-voltage interlocking structure can detect it at the first time and feed back the signal to the vehicle control unit (VCU).
After receiving the signal, the VCU will immediately take measures, such as reducing the motor power, slowing down the vehicle, and finally stopping it safely, and at the same time sounding an alarm to remind the driver. This effectively avoids serious safety accidents such as high-voltage electric shock and electrical short circuit that may be caused by the continued operation of the vehicle when the high-voltage circuit is abnormally connected.
Performance parameter
- Connector identification: Connector holes must be clearly identified with numbers, letters, etc.
- Operable space: Connectors need to be disassembled and assembled for various reasons during use, so the operable space of the connectors needs to be considered. Usually, simulation is performed in 3D software such as CATIA to determine whether it is operable.
Mechanical performance
- Connector insertion and extraction force
- The retention force of the terminal in the protective sleeve.
- The minimum pulling force between the terminal and the cable after crimping
Electrical properties
Connector anti-touch finger protection:To prevent the danger of accidental contact between human body and live parts, the device housing shall not have any holes leading to live parts except those necessary for operation, or shall be equipped with corresponding anti-electric shock protection parts.
According to ISO20653, the touch-proof requirement for common connectors is IP2XB. A jointed test finger with a diameter of 12 mm can be fully inserted, but it should be kept at a sufficient distance from the dangerous parts (the probe cannot touch the dangerous parts when the dangerous parts are moving slowly).