A brand-new production process and equipment to ensure the particle size and moisture requirements of lithium iron phosphate.
Particle size: d50=1-2um, d100<10um; (Malvern laser particle size analyzer test) Moisture: ≤600ppm (Karl Fischer moisture tester)
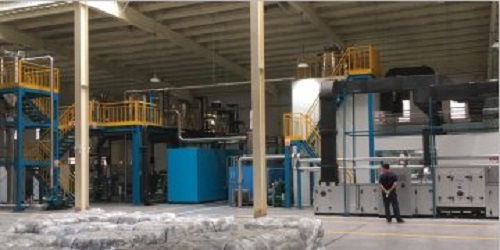
A new LiFePO4 Process Systems
LNPE iron phosphate crushing sleeve
Drying, packaging, and conveying into a processing system.
The system uses counter jet technology to combine the crushing and drying of lithium iron phosphate into one, and uses high-temperature nitrogen as the crushing and drying air source to instantaneously dry the materials, eliminating the separate drying system, and greatly reducing the production cost.
For example, the first-stage 3000 tons/year production line adopts traditional technology, and the second-stage 3000 tons/year adopts new technology.
The total annual operating cost saved by the second line is 5.5 million yuan. The entire production line adopts an anode pressure conveying system without manual connection points, and the production environment is clean and dust-free.
The high-temperature nitrogen shielded airflow pulverize developed for the lithium iron phosphate LiFePO4 industry is an inert gas (nitrogen, argon, carbon dioxide, etc. ) closed ultra-fine pulverization system with circulatory protection, the system uses high temperature gas at 120-170℃, which can instantaneously dry the materials in counter-jet.
Feature of performance
The equipment uses supersonic airflow to accelerate the material, and realizes the crushing of the material by the collision between the material.
Since the processing material is easily oxidized powder, the equipment adopts an inert gas protection system. Because the inert gas is expensive, a closed system is usually used. At the same time, strict air-tight separation devices are used at the inlet and outlet.
The external end face sealing technology (unique technology) can obtain strict particle size distribution and effectively ensure the precision of classification, suitable gas-solid concentration control technology can obtain better crushing efficiency and strict particle size distribution, and can ensure that the equipment operates stably for a long time.
Designed with a full-surface secondary air ring, so that the qualified particles stay in the crushing chamber for a short time and effectively disperse and dissociate the agglomerated powder, thereby reducing the generation of excessively fine powder and increasing the yield.
The type and purity of the inert gas (nitrogen, argon or carbon dioxide, etc.) and purity can be selected and controlled according to the requirements of the process and product characteristics, the inert gas is recycled and the loss is small.
Fully sealed negative pressure operation, pulse automatic cleaning, the collector adopts PTFE membrane filter material, the collection efficiency is >99.99%, and there is no environmental pollution.
An emergency filter and alarm device are designed behind the dust collector to prevent accidental dust from entering the compressor.
High degree of automation, the whole system adopts PLC automatic control system, which can realize one-key start and stop, automatic nitrogen supplement and pressure balance, simple operation.