Keyword: lithium battery electrode
With the rapid development of coated substrates, the rapid rise of the precision electronics industry and the new energy industry, the manufacture of modern industrial products has put forward higher and higher requirements for coating technology and coating environment, such as various flat surfaces, optical films for displays, flexible printed circuit boards, and lithium-ion battery electrodes which is related to new energy.
Compared with textiles, the film has a thinner substrate, and the temperature tolerance is different. It is more prone to wrinkles during the coating process, which brings greater challenges to the process technology.
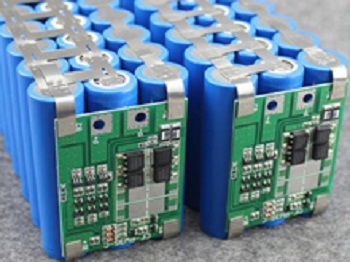
Coating of li-ion battery manufacturing
Non-parallelism of guide rollers
Solution: First, measure and observe whether the left and right diameters of a single non-parallel guide roller are the same. If they are inconsistent, you need to directly replace the guide roller; if the left and right diameters are the same, you need to adjust.
Specific adjustment method: select the reference point, first visually measure the parallelism, observe the gap between the guide rollers, and then use auxiliary tools to measure. The most practical measurement method in engineering is to use a tape measure to go around the two guide rollers to form a closed loop ellipse reading Take the perimeter and make corresponding adjustments based on the difference in data.
The installation problem of guide roller
Solution: Increase the gap between the guide rollers and reduce the wrap angle of the guide roller in the film path. The bearing of the guide roller should be lubricated on time, clean up the dirt on the surface of the guide roller in time, and keep the guide roller clean and free of foreign matter.
The problem of compound pressure
Solution: The equipment does carbon paper test regularly. Two A4 papers sandwich the carbon paper, and the lifting roller is placed at each end of the roller, and then the roller is pressed and taken out.
According to the depth of the carbon paper indentation, it is judged whether the composite pressure on both sides is the same, if they are inconsistent Need to make adjustments, the process can appropriately reduce the compound pressure, the production line is best arranged to produce products of the same width, or try to avoid arranging only narrow products for a long time, and wide and narrow products can be interspersed to arrange production
Substrate: the tension of the substrate
Solution: The substrate can be directly replaced or the unwinding tension of the substrate can be increased appropriately, but not too large.
Deformation of the substrate
Solution: Under the premise of ensuring the product’s composite fastness and drying, reduce the temperature of the hot roller or oven to ensure that the unwinding tension is reduced or not during the normal coating of the product, and the winding tension is as large as possible.
Substrate tension does not match
The wrinkles caused by this reason are mainly vertical and oblique. Causes of vertical wrinkles: The process tension is too large, it cannot be flattened during compounding, and the upper and lower substrates are wrinkled after compounding.
Causes of oblique folds: excessive tension in the process and improper correction of deviations will cause the substrate itself to have uneven tightness, uneven stress, and regular folds to the loose side.
Solution: The smaller the substrate thickness, the lower the tension, and the narrower the substrate width, the lower the tension. If this principle is not followed, wrinkles are likely to occur if the tension is not matched; constant tension unwinding and taper tension winding are the tension setting principles used in general production.
If the setting is unreasonable, it is easy to follow the roll diameter during the production process. Folds appear due to the change.
Process: Changes caused by tension fluctuations
In the actual production process, the running speed of the traction roller is generally higher than the speed of the previous section, so as to play the role of traction. If the setting is unreasonable, wrinkles will occur.
At the same time, if the substrate has longitudinal elasticity, there will be changes in elasticity due to the action of the tension roller (tracking roller) during the coating process, causing wrinkles.
In terms of equipment, large fluctuations in the operating frequency of the motor will also affect the tightness changes in the entire production process, causing wrinkles.
Solution: If the problem is the substrate itself, replace the substrate directly; if the tension is set too high in the process, reduce the tension appropriately; if it is an equipment problem, you need to maintain or replace the spare parts.
Heating temperature is too high
When the process has the setting of laminating the film after coating, due to the high heating temperature, the film will be scalded into transverse wrinkles in the transverse direction during laminating, or deformation and wrinkles will occur due to the high temperature.
Solution: lower the temperature.
The glue layer is too thick
If the adhesive layer is too thick, especially when the viscosity of the adhesive is too high, the two substrates are prone to slip and cause wrinkles after co-extrusion.
Solution: Appropriately reduce the thickness of the coating, or reduce the solid content of the coating without changing the thickness, or choose raw materials with a low viscosity of the adhesive.
In short, wrinkling in the coating process will affect the appearance, performance and end user experience of the product.
This article deals with equipment problems such as non-parallel guide rollers, guide roller installation, compound pressure, forced correction, eccentricity of the air shaft, etc., from the uneven tension of the substrate itself, the deformation of the substrate during production, and the mismatch of the tension of the substrate.
For the substrate problem, from the changes caused by the tension fluctuation in the production process, the heating temperature is too high, the glue layer is too thick and other technological problems, that is, the causes of wrinkles are analyzed in three aspects and solutions are proposed. Preventing wrinkles in the coating process is a work that requires front-line technicians and production personnel to frequently summarize the work on site.
In actual production, different products or different coating methods will cause wrinkles, and may even appear beyond the scope of wrinkles described in this article. This requires operators to observe carefully and find out early, and technicians analyze cases in time and make a summary. , So as to avoid wrinkling problems caused by various reasons, and ensure stable product quality.