Take the lead in mass production of long-cell laser machine LYH power battery equipment “take momentum”
At the moment, the world’s major power battery manufacturers have announced ambitious expansion plans.
The total planned production capacity of domestic manufacturers such as CATL, BYD, GX Hi-Tech, YW Lithium Energy, and FC Energy has exceeded 1,000 GWh; the planned production capacity of foreign companies such as LG Chem, Samsung, Panasonic, and SKI has also exceeded 500 GWh.
The “arms race” of battery giants has undoubtedly brought huge matching opportunities to lithium battery equipment companies.
More than 60%
“Demand for lithium battery equipment is strong this year, especially the power category has grown very fast, with an increase of 200% or even more than 300%.
In 2019, we will focus on consumer battery equipment. By 2021, the sales of power equipment have greatly exceeded the consumer category. Now the power equipment accounts for 60-70%.” At the “2021 International Battery Technology Exhibition”, the director of the laser business department said.
On December 1, LYH announced that it had won the bid for the FC energy lithium battery equipment project. In the previous August, it had successively won equipment orders of about 1.545 billion yuan.
In addition to FC Energy, in October this year, it also won the bid for ATL’s lithium battery equipment orders. At present, it has established long-term and stable cooperative relations with well-known manufacturers such as ATL, CATL, BYD, etc.
As of August 25, LYH’s orders for equipment in hand in the field of lithium batteries amounted to 4.554 billion yuan (tax included).
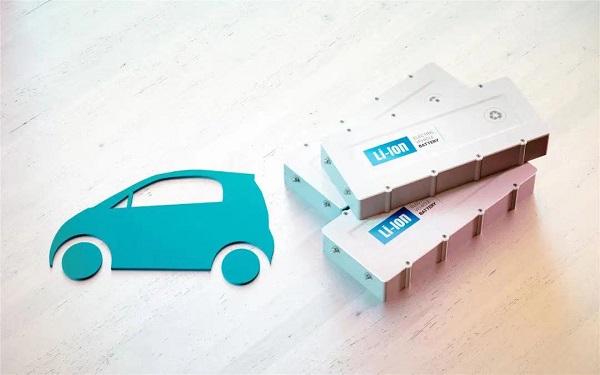
Li-Ion Power Batteries
“With the continuous increase in sales and penetration of new energy vehicles, power battery companies are accelerating their expansion, and demand for equipment purchases will explode. We expect orders for next year to grow even more than this year.”
Takes the lead in mass production
Compared with the traditional power battery, the long battery cell represented by the blade battery has the advantages of high energy density, high safety, high stability, etc., so it has increasingly become an important direction for the development of industrial technology. This year, the shipment of blade batteries has grown very fast, and leading companies such as CATL are also deploying long batteries.
Long batteries place higher requirements on manufacturing equipment. There are two main welding methods for lithium batteries, one is vertical welding from the top cover, and the other is welding from the side.
Traditional batteries are unilaterally welded. Long cells are side welded, and both ends of the shell must be welded. This requires two lasers to be synchronized to improve efficiency. Therefore, this process has a higher degree of difficulty than traditional processes.
The biggest bottleneck for long cell welding is yield and efficiency. LYH has made breakthroughs around the key technology of long-cell laser welding and launched the long-cell laser welding machine, which is at an advanced level as a whole.
The company has realized batch production of long batteries with simultaneous welding on both sides, and the production efficiency can reach more than 12PPM.
The PSO laser welding technology + CNC space trajectory control technology for side welding of square power batteries can accurately control the welding certainty of the ring spot laser in the high-speed spin welding of long-cell batteries. The stable welding speed can reach 250mm/s, which can help lithium battery manufacturers improve product quality and mass production efficiency.
Fully integrated power battery manufacturing
In addition to laser welding machines, in the field of laser equipment, it has also developed and mass-produced “Vertical-Laser Die-cutting and Slitting Machine”, “Vertical-Laser Die-cutting and Cutting Machine” and “Horizontal-Laser Die-cutting and Slitting Machine”. “And many other models have been recognized by many lithium battery companies.
The transition from winding to lamination is one of the main technological trends in lithium battery manufacturing. The cutting and stacking machine is faster and more efficient. The application in the field of consumer lithium batteries has been very mature, and the field of power batteries is already in the stage of rapid introduction.
In addition to laser equipment products, the performance of coating products is also at the forefront of the industry. The double-layer high-speed wide-width coating machine has a maximum width of 1400MM and a speed of 60-90m/min. On the basis of increasing the coating speed and amplitude, it effectively solves many difficulties in the industry.
At present, the equipment product catalog basically covers the whole process of lithium battery production, including coating and die cutting of the core making section, winding/lamination of the cell assembly section, tab welding and packaging, to the chemical composition of the cell detection section, then to the modules of the battery assembly section, the PACK automation line, etc., and the whole line integration is realized in the cell assembly line, battery assembly line and other stages.
Few makes it
At present, in the entire industry, there are not many equipment manufacturers that can connect power battery equipment across the board.
In order to better meet the needs of customers for intelligent manufacturing, the company proposes a digital intelligence whole plant solution.
The overall functional framework covers multiple stages of lithium battery production such as pole piece forming, battery cell assembly, modules, and PACK. It can help battery companies promote the upgrade of smart manufacturing from three stages, break through digital barriers from the bottom up, and achieve efficient resource allocation and lean production.