Heating can eliminate resistance? Japanese scientists break through key bottlenecks, full solid state batteries are one step closer to application
One step closer
As researchers at Tokyo Institute of Technology, the Association of Iron and Steel Technology (AIST) and Yamagata University have introduced a strategy to restore their low resistance, full solid state batteries are now one step closer to becoming the next-generation main battery.
They also explored potential reduction mechanisms, paving the way for a better understanding of the basic working principles of full-solid-state lithium batteries.
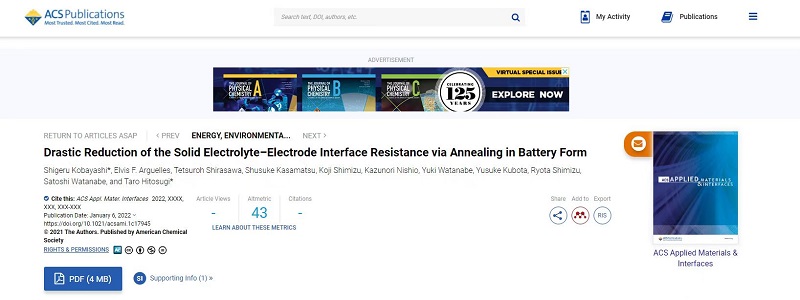
Full solid state li-ion batteries
Full-solid-state lithium batteries have become a new upsurge in the field of materials science and engineering, because traditional lithium-ion batteries can no longer meet advanced technical standards, such as electric vehicles that require high energy density, fast charging, and long cycle life.
Full solid-state batteries use solid electrolytes instead of liquid electrolytes in traditional batteries, which not only meet these standards, but also can be fully charged in a short time, so it is relatively safer and more convenient.
Challenges
However, solid electrolytes also have their own challenges.
The results show that the interface between the cathode electrode and the solid electrolyte shows a large resistance, the source of which is not yet clear. In addition, when the electrode surface is exposed to the air, the electrical resistance will increase, and the capacity and performance of the battery will decrease accordingly.
Although scientists have tried many methods to reduce the resistance, they have not been able to reduce the resistance to 10Ωcm2, which is the interface resistance value reported when not exposed to air.
Recently, a research team from Japan may finally find a way to solve the above problems. Its research results were published in the journal ACS Applied Materials & Interfaces.
The team was able to find a strategy to effectively restore low interface resistance and reveal the mechanism of resistance reduction, providing valuable insights for the manufacture of high-performance full-solid-state batteries
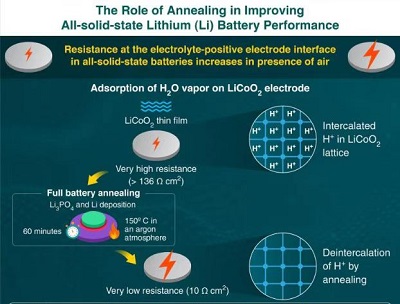
All solid state li-ion batteries
First, the team prepared a thin film battery composed of a lithium anode electrode, LiCoO2 cathode electrode and Li3PO4 solid electrolyte. Before completing the battery production, the research team exposed the LiCoO2 surface to air, nitrogen (N2), oxygen (O2), carbon dioxide (CO2), hydrogen (H2), and water vapor (H2O) for 30 minutes.
Surprisingly
To their surprise, they found that the performance of the battery exposed to N2, O2, CO2 and H2 did not decrease compared with the unexposed battery.
Professor Hitosugi said, “Only water vapor will strongly degrade the Li3PO4-LiCoO2 interface and greatly increase its resistance, which is more than 10 times higher than the unexposed interface.”
The team next carried out a process called “annealing”, in which the sample was heat-treated in the form of a battery at 150°C for one hour to deposit the anode electrode. Surprisingly, this reduces the resistance to 10.3 Ω cm2, which is comparable to an unexposed battery.
Through numerical simulations and cutting-edge measurements, the team subsequently revealed that the reduction may be due to the spontaneous removal of protons inside the LiCoO2 structure during the annealing process.
The researchers said, “Our research shows that the protons in the LiCoO2 structure play an important role in the recovery process. We hope that the elucidation of these interface micro-processes will help expand the application potential of full solid-state batteries.”