Lithium battery defects are broken one by one, new double-layer solid-state batteries target EV, energy storage and other markets
It is reported that US battery start-up Ion Storage System is currently building a production facility for its unique “double-layer solid-state battery” and plans to achieve an annual output of 10 MWh by the end of 2023, enabling large-scale commercial battery production.
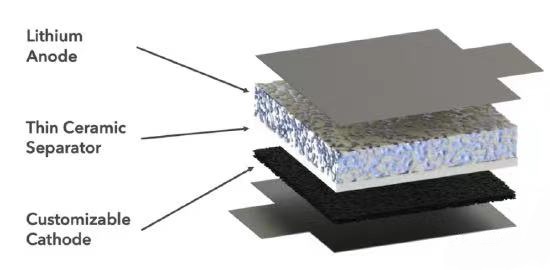
New double-layer solid-state lithium battery
Key difference
It is worth noting that the key difference between the battery the company is trying to make and other solid-state batteries is: the “double-layer design.”
This reduces some of the pitfalls of typical lithium-ion batteries and is compatible with existing and next-generation cathode chemistries, while avoiding the use of key raw materials such as cobalt, nickel and gold.
Ion Storage Systems said the product could target multiple markets, with uses ranging from defense and consumer products to electric vehicles and power grid storage.
The lithium battery contains a dense ceramic electrolyte separator, which is attached to a porous ceramic electrolyte support. This porous scaffold resembles a sponge and creates a continuous and uniform path for lithium metal plating without external volume changes.
Special structure
The dense layer acts as a solid-state separator to block lithium dendrites and avoid short circuits. Benefiting from this structural feature, the solid-state electrolyte of this lithium battery is compatible with a wide range of existing and next-generation cathode chemistries, and no flammable materials are used in the battery cell construction.
The bilayer battery architecture is made of low-cost, non-flammable materials. Because of the use of lithium metal anodes, it is possible to meet the performance criteria of next-generation batteries, including high energy density, strong cycling performance, wide temperature range, and fast charging at room temperature without compression.
The battery can utilize existing and next-generation cathode chemistries, eliminating the need for supply-constrained materials such as nickel and cobalt.
Of course, there are also some difficulties in the current process of scaling up production. Ion said that it uses existing industrial-scale ceramic preparation methods, benefiting from a unique structure that can utilize widely deployed lithium-ion battery manufacturing equipment for final battery assembly.